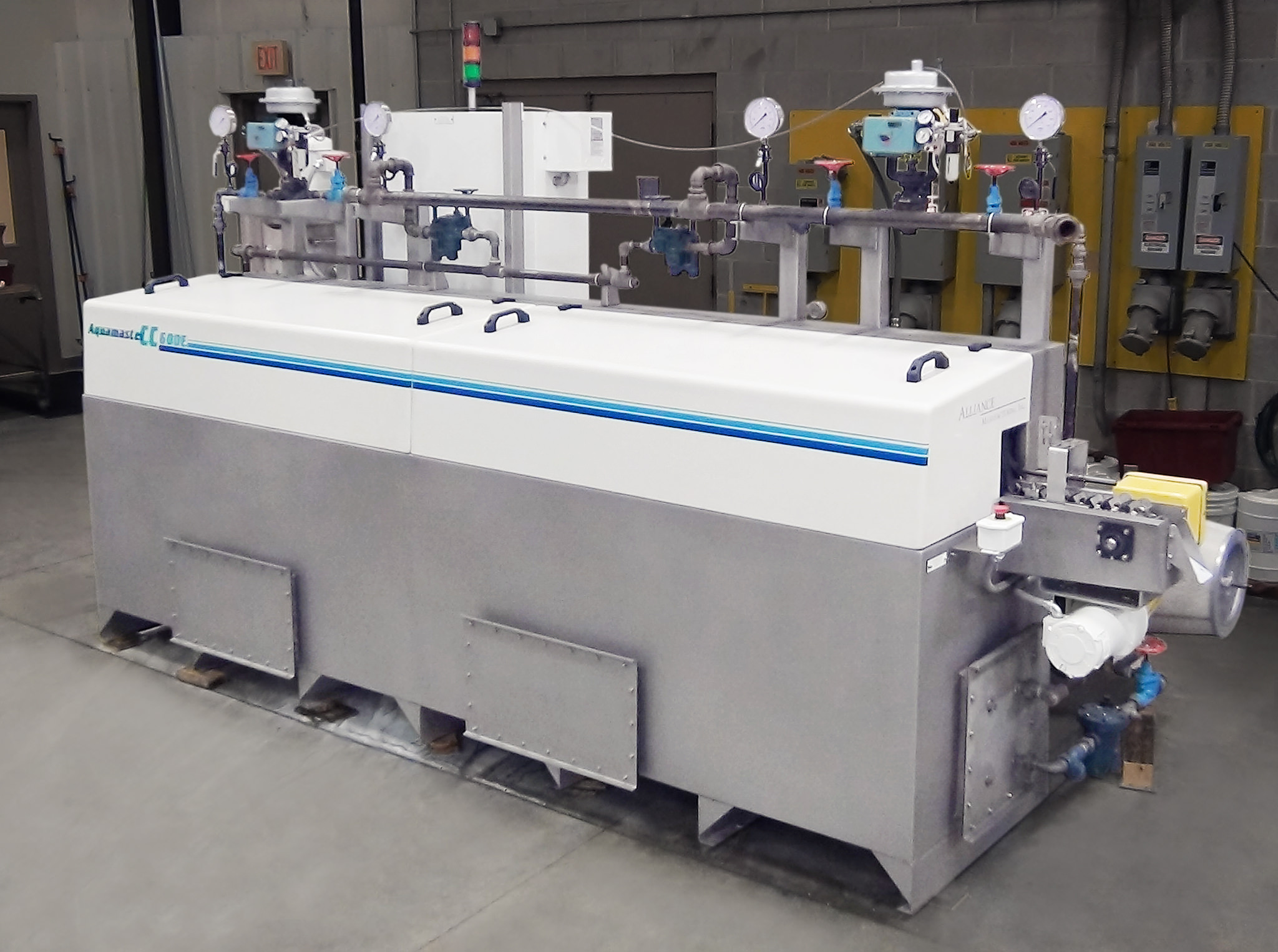
Customer Background
A leading manufacturer of medium caliber ammunition cartridge cases in brass, steel, and aluminum. Their manufacturing operations include forming, machining, finishing, and thermal treatments. They produce components for U.S. military.
Challenge
Customer was seeking a parts washer for an M-433 part that measures approximately 1.125”x1.5.” They wanted a fixture that could hold parts up to 2.5″ long. The part was contaminated with drawing lube from the manufacturing process, and had to be visually clean and as dry as possible using ambient blowoff.
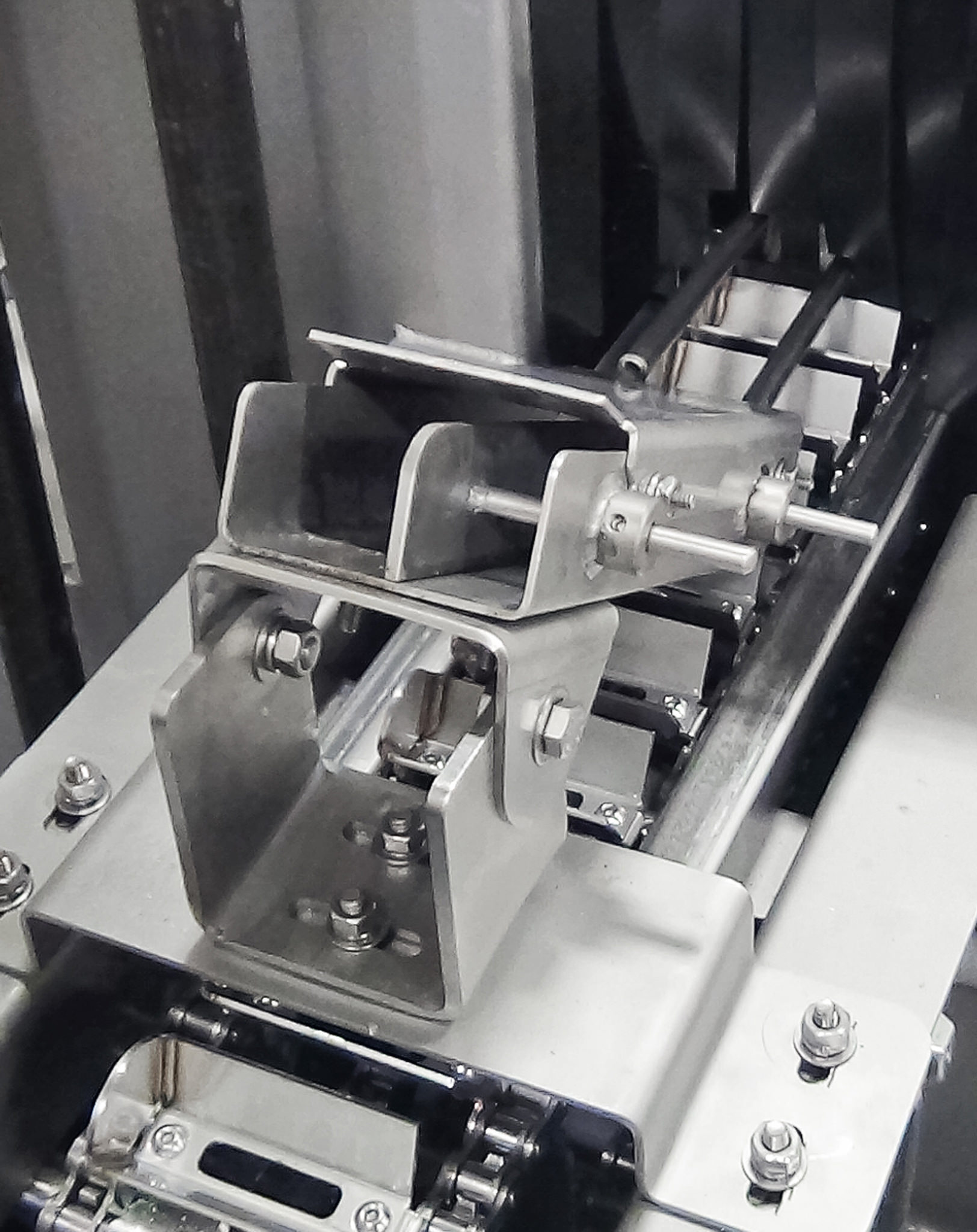
Solution
Alliance provided an Aquamaster CC-600E dual chain conveyorized parts washer with a custom-designed parts fixture for cleaning cartridges. A custom load chute was designed for automatic loading of ammunition cartridges. A magazine-style chute can be manually loaded and automatically meters parts onto the fixtures. The conveyor was designed with dual chains with fixtures that span across the chains. Conveyor speed is adjustable. An intermediate blowoff module between the wash and rinse stages strips wash chemistry from part prior to entering the rinse stage. Special wash chemistry was required for removing the drawing lube. Minimizing cross-contamination between the wash and rinse was very important. High-velocity air knives are in the last blowoff module. The cartridge cleaning machine is also equipped with an exhaust fan system and a condensate return pump. The cartridge washer is heated with steam, utilizing the customer’s onsite boiler system.