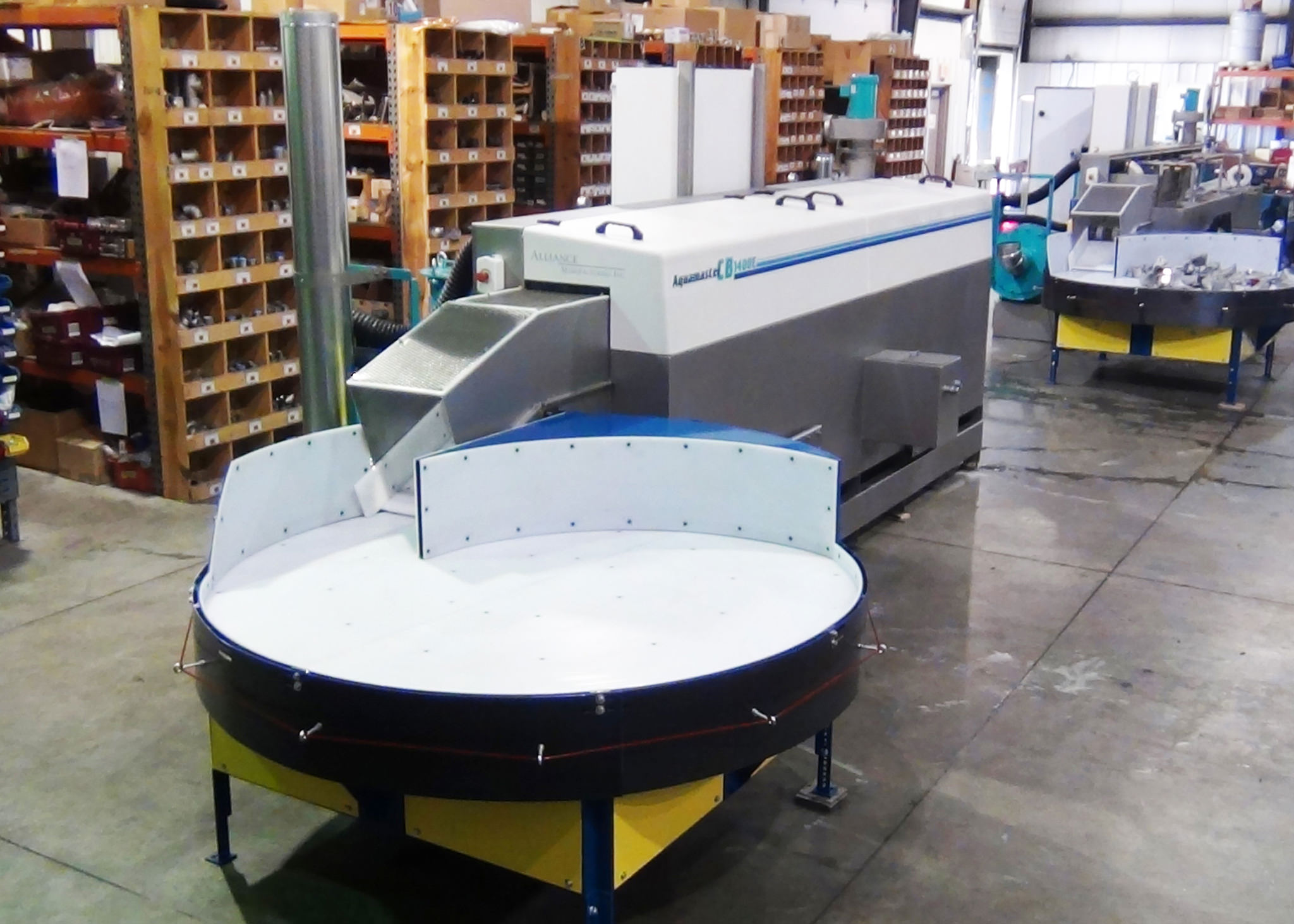
Customer Background
The customer is a Tier 1 supplier of brake systems for automotive and non-automotive manufacturers. They supply brake systems for well-known motorcycle, automotive, and ATV manufacturers with a focus on lean manufacturing processes.
Challenge
The customer was seeking a brake component part washing system to clean chips and coolant from miscellaneous aluminum manufactured parts with the largest parts measuring approximately 10ʺ x 10ʺ x 10ʺ. The washing system design was required to meet a production rate of one part every 30 seconds with the brake components exiting visually clean. Dryness was not a critical factor so residual moisture was acceptable.

Solution
Alliance provided a two-module brake component washing system consisting of wash and ambient blowoff sections. Photo-eye sensors located at the load end turn the pumps and blowers on in sequence as a part is loaded. Options included in the design were an exhaust fan system, recirculated rinse module to reduce tank volume, and an oil coalescing system. A 72ʺ counterclockwise-rotating part accumulation table was added with an unload chute on the discharge end of the machine to collect part as they exit the washer. The machine was made with a 12ʺ high product opening.
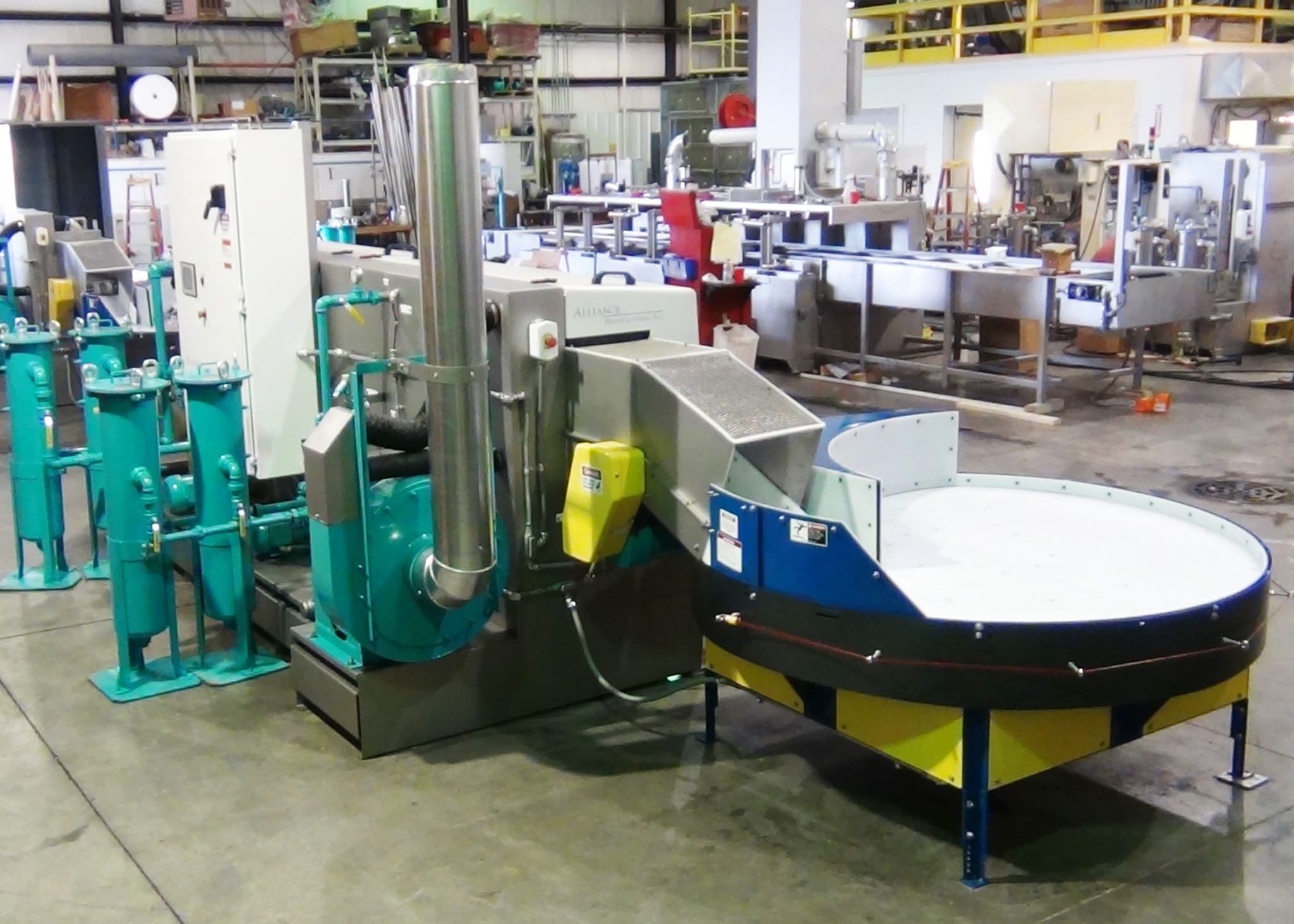