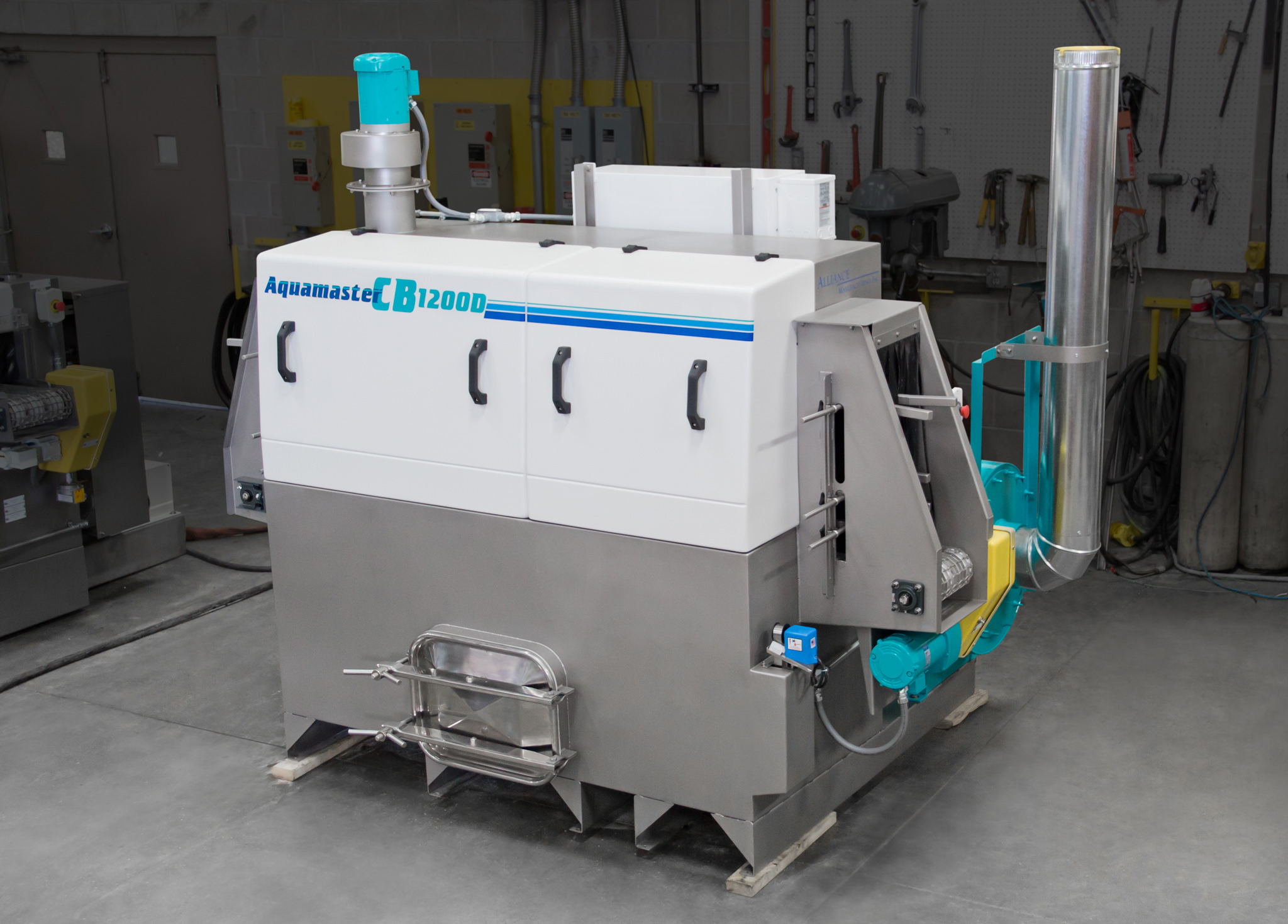
Customer Background
Customer serves the aviation and aerospace industries by producing components to enhance aircraft motion control, aircraft propulsion, and weapons system motion control. Their customers are aircraft and weapons systems manufacturers. They also focus on energy efficiency and energy management for the industries they serve. Company locations are present in 14 countries.
Challenge
The customer needed a washing system to clean off a fine coating of oil from plastic trays measuring 11.5”W x 17”L x 2’8”H. The decontaminated trays needed to be visually clean, and relatively dry, although residual moisture was acceptable. The production rate was very low at approximately 200 trays per week.
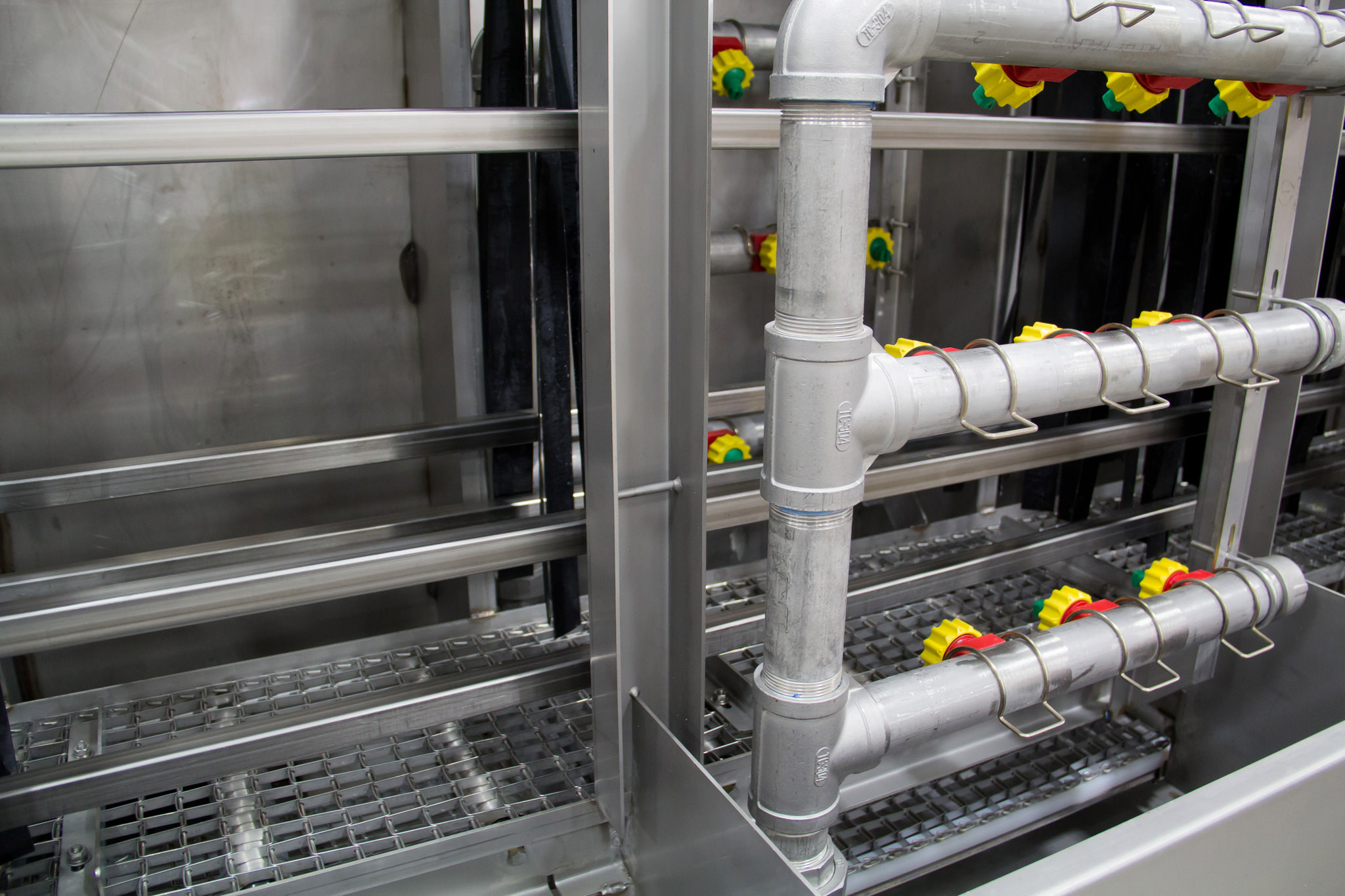
Solution
An Aquamaster CB-1200D, with wash and ambient blowoff zones was manufactured for cleaning plastic trays. Alliance’s D-Series belt washers are designed specifically for trays and returnable dunnage. Incorporating a slim and tall conveyor opening with adjustable lane guides that run the length of the machine, allow the trays to remain upright during the entire cleaning process. Product width is adjustable from 3” to 9” wide x 24” high. A 12-inch wide, flat wire stainless steel conveyor belt is supported by stainless steel rollers at a rate of approximately 1 ft/min. Clip-on adjustable spray nozzles placed on either side of the conveyor, and angled/adjustable high-velocity air knives are located on the sides and top of the conveyor to remove gross amounts of moisture. This application required the added benefits of an exhaust fan for removing steam, a micro-filtration chamber to finely filter recirculating wash solution, a 1” oil skimmer to remove floating oils, and a chemical injection system used to provide accurate detergent concentration. A sound-dampening package was also incorporated with an ambient blowoff system. Air inlet stack and unload areas are lined with noise-reducing insulation. Two segments of Alliance’s patented “Full-Access” lift-off canopy and a hinged cleanout door were included in the design for ease of cleaning and maintenance of the washer. The system was designed to be compact, with a total length of just over 9 feet and a width of just over 6.5 feet.